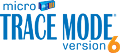 The optimal control loop tunings may save a plant huge amount of money, rising the product quality and cutting energy and material expenses. However most of control loops in industry still remain non-optimized due to the wear of equipment or process or environmental changes that occur with time. A continuous or periodical control loop tuning is required to readjust the control system to the changing process. The problem is that the new control loop tunings should be done when the control system is in operation for several years and the system integrator may not be available.
New software product is now on sale - Micro TRACE MODE 6 with adaptive control offering model free automatic calculation of the optimal control loop tunings on the live process. Micro TRACE MODE is installed onto industrial controllers and provides data acquisition and direct digital process control. The Micro TRACE MODE 6 is programmed in the handy TRACE MODE 6 Integrated Development Environment in one of the 5 IEC61131-3 programming languages.
The TRACE MODE 6 visual programming tools ensure easy development of control loop programs and the original adaptive control algorithms available in the Micro TRACE MODE 6 allow automatic calculation of the optimal PI, PID and PDD loops tunings on the live process.
The adaptive control library available in TRACE MODE 6 contents the following algorithms:
- Adaptive PID control (APID);
- Adaptive PDD control (APDD);
- Adaptive PID loop tuning at major setpoint change (RJMP);
- Model identification (IDNT);
- Identification based adaptive PID loop selftuning (CALC);
- Modal control (MREG).
The TRACE MODE APID adaptive control algorithm is suitable for processes with proportional output devices (actuators), meanwhile the APDD algorithm is for the integral actuators with constant or variable execution time. Both algorithms operate in two stages: at the first stage a small amplitude test sinusoidal signal is added to the control output. The algorithm analyses the process response to oscillations and determines the control loop tunings that provide the desired phase lagging. At the second stage the oscillation generator and adaptive control switch off and the optimal tunings are applied to the loop. Such selftuning may be run periodically or even continuously, ensuring automatic tuning of control loops.
The TRACE MODE RJMP adaptive control algorithm provides automatic PID loop selftuning at every setpoint change on the live process. Usually 3-4 small setpoint changes are enough to tune the control loop to the optimum. This adaptive control algorithm is fast, easy and intuitive.
The TRACE MODE modal control loop available in the Micro TRACE MODE may operate in noisy environments and it is 2-3 times faster than a well tuned PID loop.
All Micro TRACE MODE adaptive control algorithms may be emulated and debugged online in the TRACE MODE Integrated Development Environment editors.
The Micro TRACE MODE contents built-in drivers for several PLCs and has an open driver format for driver development in the C language.
A PLC programmed in TRACE MODE, can be easily connected to the operator interface PC run under TRACE MODE SCADA/HMI via the built-in I-NET and M-LINK protocols. In this case both PLC and SCADA databeses will be integrated, cutting engineering time and eliminating errors. The Micro TRACE MODE can be also connected to the third parties SCADA/HMI via the OPC server. |