Zaporozhye Aluminium Smelter (ZAS) is one of the biggest plants on the territory of Ukraine. In its operation, the plant relies on the implementation of new technologies and developments. One of the latest implementations at the plant is the “Compressor Station” control system developed by HARTRON-CONSAT Science & Production Enterprise (S&PE) (Ukraine).
The compressor station task is to provide a failure-free supply of compressed air with the pressure from 5.8 to 6.2 kgf/cm2 (580-620 kPa) to main and auxiliary shops of the plant. The main compressor station equipment of the aluminium shop comprises six K-250 type turbo compressors, three 1BB-40/9 compressor plants and one screw compressor.
This project is based on the integrated SCADA/HMI & Softlogic system TRACE MODE and performs the following tasks: ° automatic and supervisory process control; ° notification of operating personnel about emergency situations by a sound siren; ° processing of analogue signals from the position of program filtration and smoothing; ° logging the information about water and power consumption for each compressor and for the whole station as well as the downtime for each turbo compressor; ° generation and printout of reports, requested by operator.
The figures given below show air pressure behavior diagrams before implementing the control system:
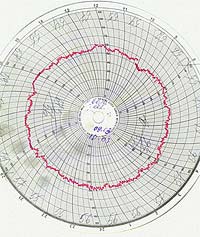
and after the control system implementation: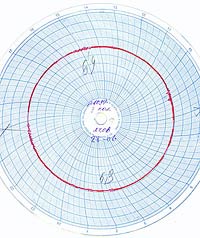
The development and implementation of the “Compressor Station” control system have been carried out during 9 months. The developer group has consisted of a leading project engineer, 5 engineers from the HARTRON-CONSAT S&PE’s Schematic Design Department. The developers note that integrated TRACE MODE algorithm libraries have allowed to considerably reduce the system development lead time. |