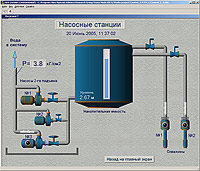 The Nestle "Altay" confectionery (Barnaul city, Russia) has finished setup works for the heat and water supply shop control system. The new system is fully developed by the factory engineers in the TRACE MODE 6 SCADA/HMI development system.
The new control system includes HMI for 8 screens, controlling the following equipment:
- pumping plants and boiler;
- air and и refrigerator-compressor shops;
- sewage pumping plant;
- preparation shop;
- input ventilation;
- exhaust ventilation;
- industrial air conditioners.
The following «Owen» made PLC were used in the project:
- 8 channel thermoregulators ТРМ138;
- I/O modules МВА8;
The new system has a simple structure: an HMI PC run under TRACE MODE 6 is connected to the PLCs through RS 232/485. The PLCs collect data on the temperature, pressure, levels, equipment status etc from various shops of the confectionery. The logical program for process control and alarming is written on the visual FBD language - one of the five IEC 6-1131/3 standard programming languages supported in TRACE MODE 6.
The new system has a distributed structure - the controlling devices are distributed over large territory.
The system developer, Mr. Yury Navodkin, control engineer at the Nestle Altay Confectionery estimates that the new control system will result in a significant reduction of time expenditures for detection and repair of the process equipment failures, and the overall maintenance cost reduction. |